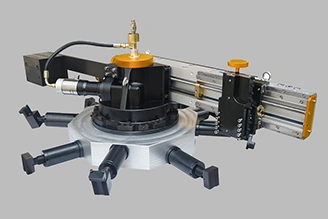
# Flange Facer Machine: Essential Tool for Precision Flange Resurfacing
## What is a Flange Facer Machine?
A flange facer machine is a specialized tool designed for resurfacing and machining flange faces to ensure proper sealing and alignment in piping systems. These machines are crucial in industries where flanged connections are common, such as oil and gas, petrochemical, power generation, and shipbuilding.
## Key Features of Modern Flange Facers
Modern flange facer machines come equipped with several important features:
– Portable design for on-site machining
– Precise cutting capabilities
– Adjustable cutting speeds
– Compatibility with various flange sizes
– Durable construction for industrial environments
## Applications of Flange Facing Machines
These versatile machines are used for:
– Repairing damaged flange surfaces
– Preparing new flanges for installation
– Creating proper surface finishes for gasket seating
– Removing corrosion and pitting from flange faces
– Ensuring flatness and proper alignment of mating surfaces
## Benefits of Using a Flange Facer
Investing in a quality flange facer machine offers numerous advantages:
– Cost savings by repairing rather than replacing flanges
– Reduced downtime during maintenance
– Improved safety by ensuring proper sealing
– Increased system reliability
– Compliance with industry standards for flange surfaces
Keyword: flange facer machines
## Types of Flange Facing Machines
There are several types of flange facers available:
### 1. Portable Flange Facers
These lightweight machines can be easily transported to job sites and mounted directly onto the flange for on-site machining.
### 2. Stationary Flange Facers
Larger, more powerful machines designed for shop use where flanges can be brought to the machine for resurfacing.
### 3. CNC Flange Facers
Computer-controlled machines offering the highest level of precision and repeatability for critical applications.
## Choosing the Right Flange Facer
When selecting a flange facer machine, consider:
– The size range of flanges you need to machine
– The materials you’ll be working with
– Required surface finish quality
– Portability needs
– Available power sources at your work sites
## Maintenance Tips for Flange Facers
To ensure optimal performance and longevity:
– Regularly clean and lubricate moving parts
– Inspect cutting tools for wear
– Check alignment periodically
– Store properly when not in use
– Follow manufacturer’s maintenance schedule
## Industry Standards for Flange Facing
Quality flange facer machines help achieve compliance with important standards such as:
– ASME B16.5
– API 6A
– ANSI B16.47
– MSS SP-44
– ISO 7005
## Future Trends in Flange Facing Technology
The industry is seeing advancements in:
– Automated alignment systems
– Improved cutting tool materials
– Enhanced portability features
– Integrated measurement systems
– Smart monitoring capabilities
A quality flange facer machine is an essential investment for any operation that relies on flanged connections. By maintaining proper flange surface conditions, these tools help prevent leaks, ensure system integrity, and reduce maintenance costs over time. Whether you choose a portable unit for field work or a stationary machine for shop applications, selecting the right flange facer for your specific needs will pay dividends in improved performance and reliability.