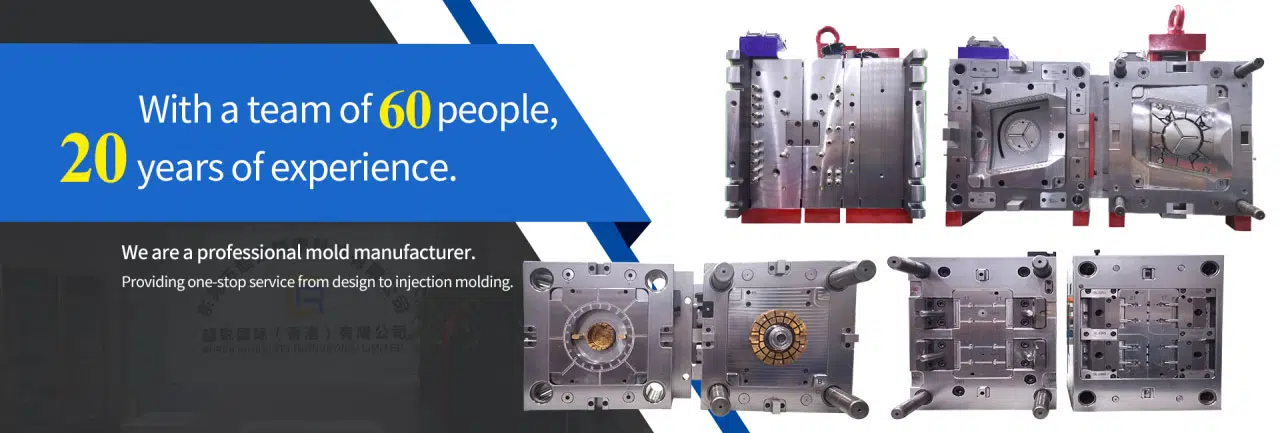
# High-Precision Machining: Achieving Unparalleled Accuracy in Manufacturing
## The Essence of High-Precision Machining
High-precision machining represents the pinnacle of manufacturing technology, where tolerances are measured in microns and surface finishes approach perfection. This specialized field combines advanced machinery, cutting-edge tooling, and meticulous process control to produce components with exceptional dimensional accuracy and geometric consistency.
## Key Technologies Enabling Precision Manufacturing
CNC Machining Centers
Modern computer numerical control (CNC) systems provide the foundation for high-precision machining, offering repeatable accuracy down to ±0.005 mm or better. These systems integrate sophisticated feedback mechanisms and thermal compensation to maintain precision throughout extended production runs.
Ultra-Precision Grinding
When conventional machining reaches its limits, precision grinding takes over. Using diamond or cubic boron nitride (CBN) wheels, this process can achieve surface finishes as fine as Ra 0.025 μm and dimensional tolerances within ±0.0001 inches.
Electrical Discharge Machining (EDM)
EDM technology, particularly wire EDM and sinker EDM, enables the production of complex geometries in hardened materials with tolerances as tight as ±0.002 mm, making it indispensable for mold making and aerospace components.
## Applications Across Industries
Aerospace and Defense
The aerospace sector demands components that can withstand extreme conditions while maintaining perfect fit and function. High-precision machining produces turbine blades, fuel system components, and structural elements with the required reliability.
Medical Device Manufacturing
From orthopedic implants to surgical instruments, medical applications require biocompatible materials machined to exacting standards. Precision machining ensures proper fit, function, and longevity of these life-critical devices.
Automotive Performance Parts
High-performance engines and transmission systems rely on precisely machined components to achieve optimal power output, fuel efficiency, and durability under demanding operating conditions.
## Challenges in High-Precision Machining
Thermal Management
Heat generation during machining causes tool and workpiece expansion, potentially compromising accuracy. Advanced cooling systems and thermal compensation algorithms help mitigate these effects.
Keyword: High-Precision Machining
Tool Wear Monitoring
Even microscopic tool wear can affect machining precision. Modern systems incorporate real-time monitoring and automatic tool compensation to maintain consistent quality.
Material Stability
Certain materials exhibit dimensional changes after machining due to internal stresses. Proper material selection and stress-relieving processes are essential for maintaining long-term dimensional stability.
## Future Trends in Precision Manufacturing
The future of high-precision machining lies in the integration of artificial intelligence, advanced metrology, and adaptive control systems. Machine learning algorithms will predict and compensate for potential errors before they occur, while quantum metrology may push measurement accuracy to new frontiers. As industries continue to demand higher performance from smaller components, high-precision machining will remain at the forefront of manufacturing innovation.